Industrial pump control
The control of industrial pumps is an essential aspect in many industrial applications.
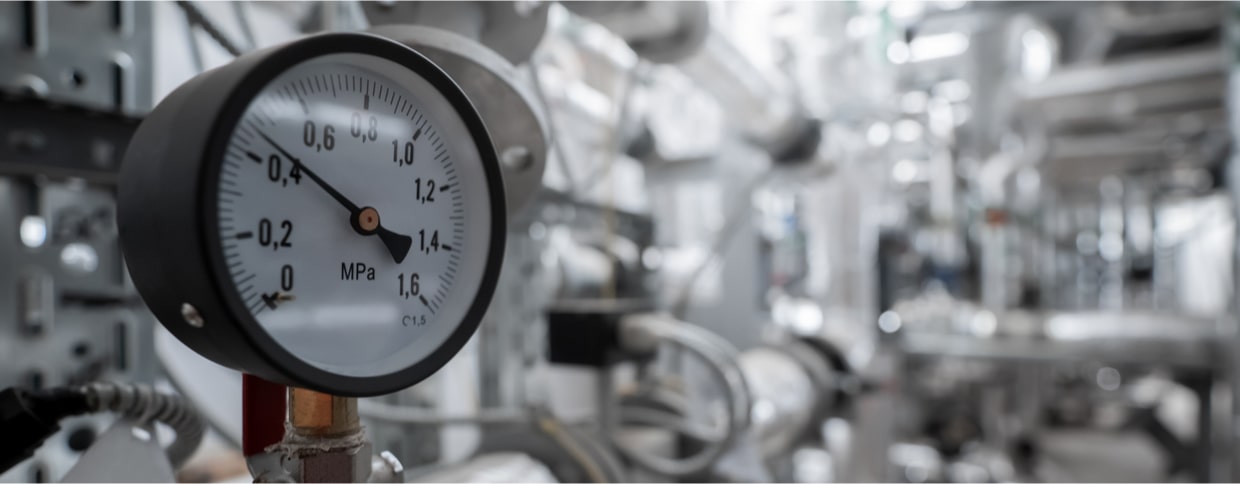
Die controller of industrial pumps is an important aspect in many industrial applications.
At the present time, in the industry numerous pumps are used to pump liquids or gases. The control of these industrial pumps is of great importance as it ensures smooth operation and efficiency The plants guaranteed.
About our industrial pump
The control of pumpsystem wobble ring pump For example, covers various aspects. First of all, it is important to determine the optimal operating point of the pump. This depends on various factors, such as the desired flow rate, pressure and viscosity of the pumping medium.
In order to optimize the operating point, various Control techniques used.
Another important component of controlling a wobble ring pump is monitoring the operating parameters. These include, for example, the temperature, the pressure and power consumption of the pump. By regularly monitoring these parameters, potential problems can be identified and resolved at an early stage.
In addition to monitoring and controlling the pump, the servicing an important aspect. Regular inspections and maintenance work ensure optimal power and pump life.
Find out more about our wobble ring pump in our product brochure.
How is a pump controlled?
A pump can be controlled in various ways, depending on the requisitions and the intended use. As a rule, a pump is controlled either manually or automatically.
At the manual Control, the pump is operated directly by one person. This can be done, for example, by pressing a switch or a button. The person can switch the pump on or off and adjust the speed or pressure if necessary.
At the automatic Control, on the other hand, the pump is controlled by a control system. Sensors are usually used here to measure the liquid level or pressure. This information is then passed on to the control system, which controls the pump accordingly. For example, this may mean that the pump is automatically switched on when the liquid level falls below a certain level. However, it can also mean that the pump automatically adjusts the speed to maintain the desired pressure.
There are also more advanced control systems based on programmable logic controllers (PLCs) are based. These enable even more precise control of the pump and can automate complex processes. With a PLC, for example, pumps can be switched on and off in a specific order or different pumps can be controlled simultaneously.
The precise control of a pump depends on various factors. These can be, for example, the type the pump, the desired intended use and the specific requisitions be of the system. It is important to select the correct control method to ensure efficient and reliable pumping function.
How does a pump control work?
There are various types of pump controls that are used in industry. One commonly used method is to use frequency inverters. These devices make it possible to control the speed of the pump and thus adjust the flow and pressure of the pump operation. In addition to frequency inverters, inverter pump controls are also a common solution. By using inverters, pumps can be precisely controlled, which enables even more precise adjustment of output.
The pump control technology can also be used via various sensors take place that monitor pump operation. For example, flow sensors can be used to measure the current flow of the pump. Pressure sensors can monitor the pressure in the line and ensure that it remains within the desired limits.
Another way to control industrial pumps is to use Pressure regulators. These devices monitor the pressure in the line and adjust the pump output accordingly. In this way, the pressure can be kept constant and an overload of the system can be avoided.
In addition to controlling the pump output, the surveillance the pump status is of great importance. Various sensors are used here, which measure, for example, the flow rate, the temperature or the vibration of the pump. Through continuous monitoring, potential problems can be identified at an early stage and appropriate measures can be taken to prevent failures or damage.
Another important aspect of pump control is automation. By integrating control systems and programming, industrial pumps can be controlled automatically. This enables efficient and reliable pump control without the need for human intervention.
German industry uses various technologies and standards for pump control. For example, the Profibus technology frequently used to facilitate communication between machines and computers to produce. This ensures seamless integration and effective control of the pumps.
The control of industrial pumps plays an important role in various industries. These are, for example, the chemical industry, the food industry and the water and waste water industry. Efficient pump control enables companies to optimize their processes, save energy and increase productivity.
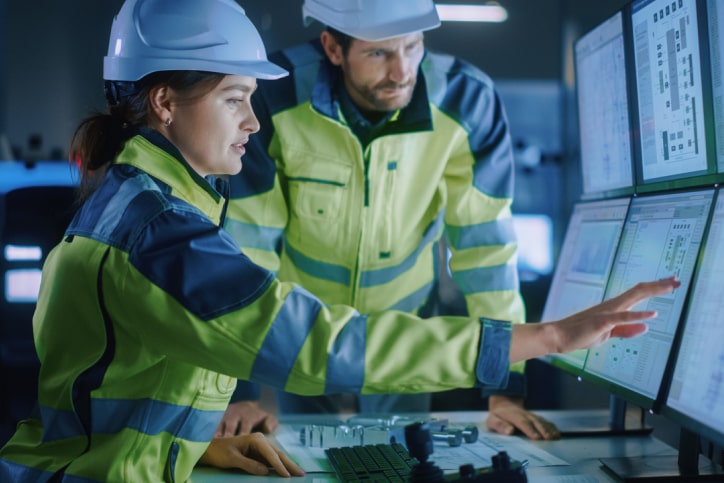
What is an inverter pump control?
An inverter pump control is an advanced technology that is used in water supply and sanitation. It enables precise control and regulation of pumps in order to consumption to optimize and the energy efficiency to improve.
This type of control is based on a Inverter, who the rpm and power Adjusts the pump continuously. By adapting the speed to actual demand, energy consumption is reduced and the life of the pump is extended.
The inverter pump control also provides precise pressure control to water flow adapt according to requirements. This enables a constant supply and prevents pressure peaks or drops.
In addition, the inverter pump control also offers a variety of Protection features. It automatically detects overloads, dry running or other operating faults and protects the pump from damage.
How does a pump pressure switch work?
A pump pressure switch consists of a pressure sensor unit and a switching device.
The pump pressure switch works on the basis of the difference in pressure in a liquid line. When the pressure falls below a certain threshold, the switch is activated and the pump is switched on. As soon as the pressure reaches the set maximum value, the switch is deactivated and the pump is switched off.
The pressure sensor unit consists of a pressure sensor and a membrane. When the water pressure drops, the membrane moves and presses on the pressure sensor. This detects the pressure drop and sends a signal to the switching device.
Die switching device consists of a relays and a switch contact. When the pressure sensor sends the signal to the relay, the relay switches on the switch contact and the pump is activated. As soon as the pressure reaches the maximum value, the relay switches off the switch contact and the pump is switched off.
The pump pressure switch makes it possible to automatically regulate the pressure in a line. This is particularly useful for maintaining constant pressure in industrial applications.