Pumps for the production of paints and varnishes
Pumps are essential for the production process and for implementing recipes for paints and paints.
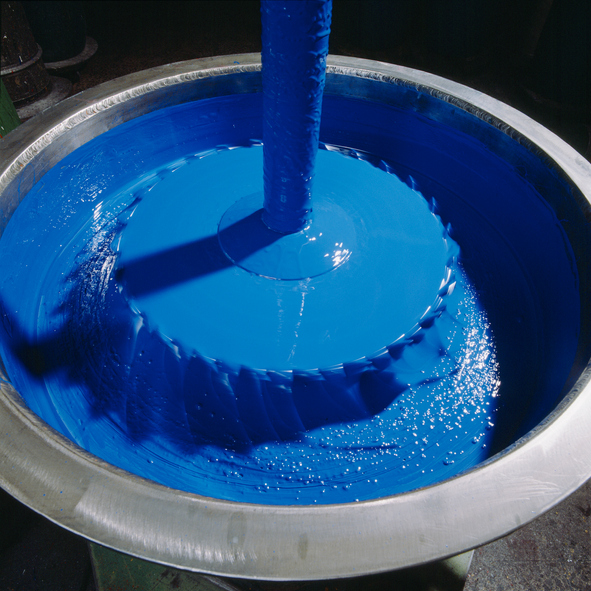
The production process the production of paints and Lacken always follows the same pattern. It consists of preparation, dissertation, completion, nuancing, quality review, approval and finally filling and subsequent shipping. During paint production, the components are particularly affected by gloss, adhesion, viscosity on. Pumping paints and varnishes with petrochemicals or solvents must therefore be able to meet and combine a wide range of requirements.
What is the role of pumps in the production of paints and varnishes?
They make a significant contribution to binding - and solvent can be transported during the manufacturing process. pumps ensure that the materials are directed to the right locations and ensure that the chemical reactions take place efficiently.
Pumps also help to transfer paints and varnishes to the desired consistency by continuously diluting the mixtures. They ensure that the paints and varnishes are kept in the containers in the right quantity and concentration. As a result, the quality of the end product can be kept at a constant level.
Pumps for paints and varnishes
They prevent paints and varnishes from being stored for too long, leading to color changes can lead. In addition, pumps make it possible to control the consistency of paints and varnishes. They do this by controlling the concentration of the various ingredients, which improves the quality of the final product.
For example, the pump type of the centrifugal pump. This pump offers very precise dosing and a high level of control, making it an ideal choice for conveying paints and varnishes. It has a closed housing to protect the pump system from the ingress of liquids or other pollutants. In addition, the centrifugal pump has a special, suitable for application adapted design. This enables better efficiency and lower energy consumption. Maintenance is also easier, as most components are easily accessible and replaceable. The disadvantages of centrifugal pumps are that they are relatively expensive, loud and difficult to maintain. They also tend to cause blockages and reduce performance during irregular maintenance.
Here comes the pumping technology of positive displacement pumps into the game as manufactured by pumpsystems. They are powerful and durable. They can be used over long periods of time and are also capable of heavy liquids to process. In addition, they are easy to handle and offer high efficiency when conveying and processing paints and varnishes. Even with High viscosities pumping media is the delivery rate reliable and continuous.
With our wobble ring pump are the requirements for the production of paints and varnishes professionally covered.
Our wobble ring pump is easy to use and is subject to strict quality controls to ensure that it meets the highest standards. It is robust, durable and can handle a wide range of liquids. With a simple yet powerful pump, high production rates and high product quality are guaranteed. In our detailed product brochure, you will find the right answer to all your questions.
How are paints and varnishes produced?
Pumps are under constant stress during the process of manufacturing paints and paints. It starts with planning and presenting. In this process, the color pigments and fillers are mixed and processed into a liquid phase. Parts of it are connective, solvents and required additives. These can be aids, such as defoaming agents or wetting and dispersing agents.
The binders in paints or varnishes ensure that pigments and other substances are bound together. They are not volatile and are still available after painting on the surface. They exist both as inorganic and organic compounds. Solvents make it possible to produce a solution of certain substances without a chemical change in the structure. Within a lacquer, they help to process and dry the paint. After processing, the evaporates solvent completely. As the name suggests, defoamers ensure that the paints and varnishes do not foam during processing. This is done through an interface between the liquid and gaseous paint film. This surface prevents gas bubbles or air injections, which lead to foam formation.
All of this is now becoming a homogeneous Mass processed. This is followed by pre-dispersion. Pre-dispersion is the most important step in preparation and is carried out by the dissolver. The dispersion process, also known as the milling process, involves the decomposition of the larger particles into smaller particles. These can then be more easily converted into the solution. Dispersion increases the solubility of the substances and improves the compatibility between the components. Dispersion is normally achieved by the action of a mechanical force field, such as an agitator. After dispersion, the solution must be brought to a constant concentration and viscosity to obtain the desired results.
This is followed by completion, adding missing raw materials and semi-finished products (e.g. binders, additives, solvents, etc.). These are dosed in such a way that the desired properties of the mixture are achieved. After completion, the mixture must still be homogenized before it is processed into end products or Further processing can be delivered. During this phase of production process Failures can occur in product production due to failure to comply with the additional sequence, incorrect dosing or incorrect homogenization processes.
This is followed by nuancing, setting the correct, desired shade. Corrections may be made here.
This is followed by quality testing and approval, as well as the filling of the finished paint.
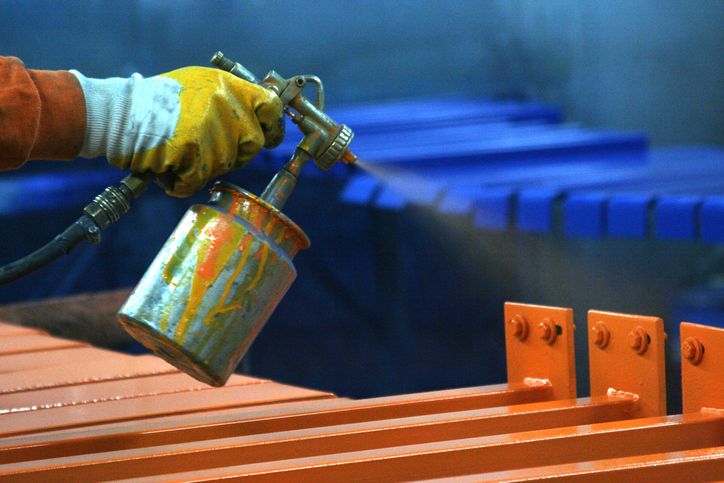
Which parts of paints and paints originate in petrochemicals?
The main components of paints and paints originate in chemical industry, in particular solvents, resins, pigments and additives.
In the petrochemicals There are many different components that are used in paints and paints. These include various solvents such as ethylene, propylene, toluene and xylene, plasticizers such as phthalates, pigments and fillers, resins and paint additives. All of these components have their origins in petrochemicals and help to maintain paint and paint quality.
These components are combined in different ratios to obtain the best possible mix. Even the composition The additives are of crucial importance. This ensures that the paints and varnishes are weather-resistant and achieve good adhesion. In addition, various additives can be used to improve the durability and resistance of the paint.
The use of petrochemicals is currently essential in order to achieve the best quality and durability from paints and paints. Thanks to the progressive development of petrochemicals, it is possible to constantly improve the properties of paint and paint products.