Output of a pump
The performance of industrial pumping systems plays a major role in ensuring efficient and reliable operation.
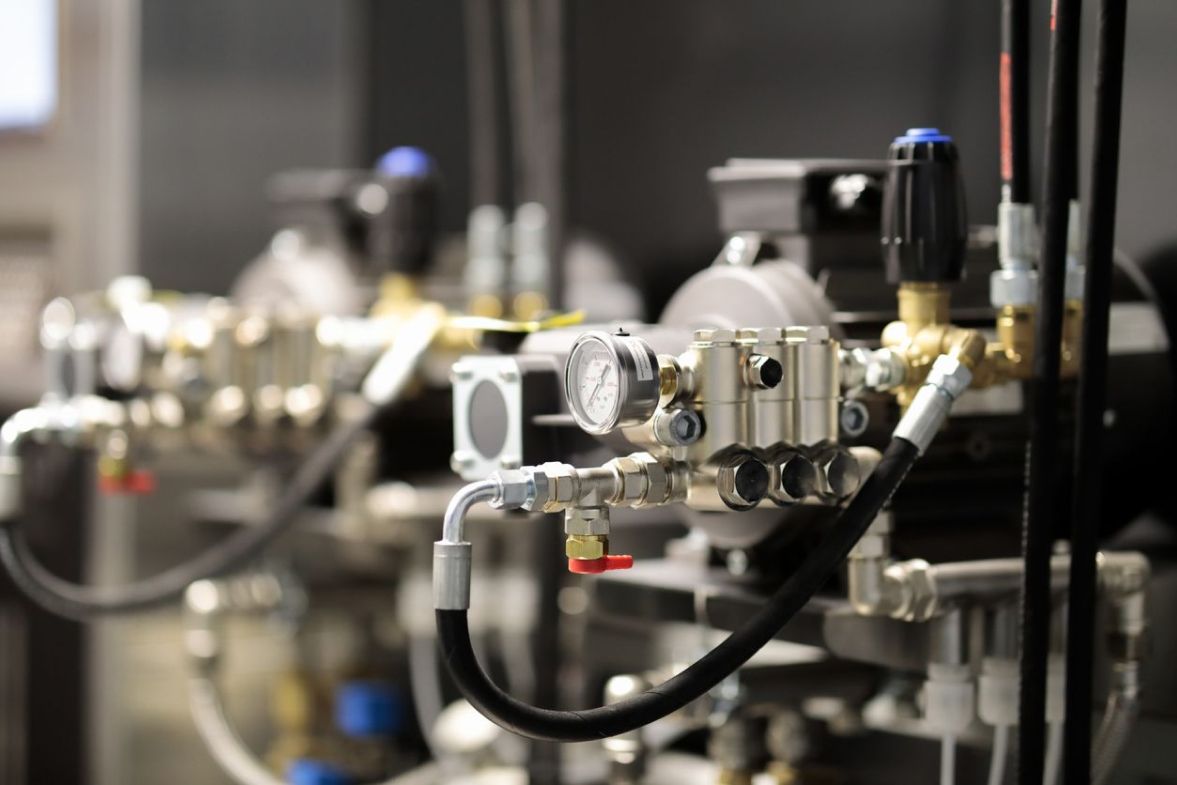
Pumping systems play an important role in numerous industrial processes and enable liquids and gases to be pumped in a wide variety of ways areas of application. The performance These pumps are of paramount importance to ensure efficient and reliable operation while maintaining to optimize energy consumption.
Die wobble ring pump In recent years, it has become a preferred choice in numerous industrial sectors developed. Its functional principle and efficiency make it a good solution for demanding conveying applications. The performance of the wobble ring pump is determined by the interaction of two main components: the wobble ring and the cells.
About our powerful pump
The wobble ring is a rotating element that moves eccentrically within a housing. It is equipped with a certain number of cells, which increase and decrease during the rotation of the wobble ring. These cells are connected to inlet and outlet openings that allow fluid to flow.
The operation of the wobble ring pump is based on the principle of volume displacement. When the wobble ring rotates, the cells enlarge and create a negative pressure that draws the liquid into the pump. As soon as the cells shrink in size, the liquid is compressed and expelled through the outlet port.
There are several benefits to this type of pump. On the one hand, it enables a continuous and pulsation-free flow of liquid, which is particularly important when conveying sensitive or viscous media. On the other hand, the wobble ring pump is very efficient, as it offers a high flow rate with low energy consumption.
In addition, the wobble ring pump is versatile and can be used in various industries, such as the chemical, food and pharmaceutical industries. It is also suitable for applications with high pressure requirements and can handle aggressive or abrasive media.
What is the performance of a pump and how is it defined?
The performance of a pump refers to its ability to deliver liquids or gases. It indicates how much volume the pump can move per unit of time. The benefit is usually in cubic meters per hour (m³/h) or in liters stated per minute (l/min).
The performance of a pump depends on various factors such as Pressure difference between inlet and outlet, the efficiency of the pump and the aerodynamic properties of the pumped medium. The higher the pressure difference and the efficiency of the pump, the greater the performance and reliability.
The performance of a pump can be defined in various ways. One possibility is electrical power consumption, i.e. the amount of electrical energy that the pump needs to do its job. This is used in the unit watts (W) measured. Another option is mechanical power, which indicates how much work the pump does per unit of time. This is measured in watts or kilowatt (kW) measured.
It is important to calculate the performance of a pump carefully to ensure that it meets the requirements of the application. If the output is too low, the pump may not have an adequate flow rate achieved, while too high performance can lead to unnecessary fuel consumption.
How do you calculate the power of a pump?
The performance of a pump can be calculated in various ways. A common method is to use the formula: power (in watts) = delivery height (in meters) * flow rate (in cubic meters per second) * density of the pumped medium (in kilograms per cubic meter) * acceleration due to gravity (in meters per second squared).
To calculate the output of a pump, the first step is Suction height be known. This is the difference in height between the point where the medium is delivered and the point where it is transported.
The volumetric flow Indicates how much volume of the medium is transported per second.
Die density of the medium is the mass per unit volume and depends on the type of medium being pumped.
Die acceleration due to gravity is a constant and is approximately 9.81 meters per second squared.
What is the nominal output of a pump?
Die nominal power A pump is the maximum output that it can deliver under certain operating conditions. It is often expressed in kilowatts (kW) or horsepower (hp). The nominal output is an important parameter for evaluating the performance and efficiency of a pump.
The nominal output is calculated based on the maximum flow rate and the maximum pressure build up of the pump. The higher the flow rate and the pressure difference, the higher the nominal output of the pump.
However, it is important to note that the rated output is not necessarily the actual output that the pump provides under all operating conditions. Actual performance may vary depending on operating point, pump efficiency, and other factors.
The nominal output of a pump is an important criterion when selecting a suitable pump for a specific application. It is important that the pump technology has sufficient nominal output to provide the required pressure and flow rate for the application. Undersizing the pump can result in inefficient operation or even pump failure.
What is hydraulic power?
Die hydraulic Performance refers to the ability of a hydraulic system to do work. It measures the amount of work or energy that is converted per unit of time in a hydraulic system. Hydraulic power is usually measured in kilowatts (kW) or horsepower (hp).
In a hydraulic system, power is determined by pressure and volumetric flow Definitely. The pressure is usually measured in bar or pascal and indicates the force with which the Fluid acts on the components of the system. The flow rate indicates how much fluid flows through the system per unit of time and is usually measured in liters per minute or cubic meters per hour.
Hydraulic power is often used to efficiency to evaluate a hydraulic system. The higher the hydraulic output, the more work the system can do. Higher hydraulic output can, for example, mean that machines can work faster and move larger loads. However, it is important that the performance meets the requirements of the application, as too high performance could result in excessive wear or damage to the components.
Various measures can be taken to optimize the hydraulic performance of a system. This includes, for example, the selection of components with higher efficiency, the minimization of leakages in the system and the use of appropriate Control techniques. A regular servicing and testing the system is also important to ensure that it is working optimally and that hydraulic performance can be maintained.
What does Q mean for a pump?
Q stands for the flow rate a pump. It indicates how much liquid can be transported by the pump per unit of time. The unit for Q is usually liters per minute or cubic meters per hour. The flow rate is an important parameter that must be considered when choosing a pump, as it influences the performance and efficiency of the pump. The higher the Q values of a pump, the higher its flow rate. It is important to determine the required flow rate according to the requirements of the application to ensure that the pump is able to perform as desired.
How can you optimize the performance of a pump?
The performance of a pump can be optimized through various measures. For example, the use of efficient pumps or the optimization of the aerodynamic properties of the system can result in higher performance. Regular maintenance and inspection of the pump is also important in order to ensure its optimal efficiency to ensure. Find out more about the Maintaining a pump in our last article.
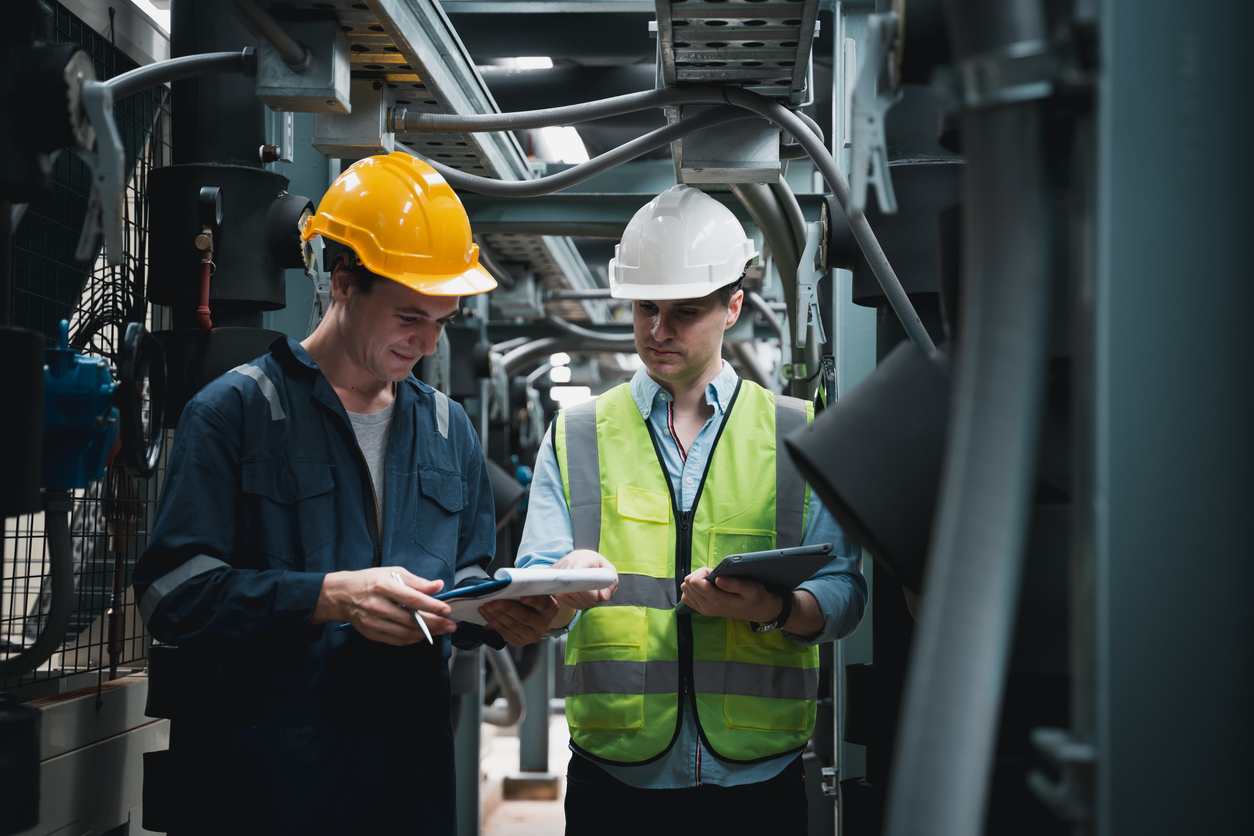
Another way to optimize performance is to use the pump pressure to optimize. Here, the pressure level can be adjusted to the specific requirements of the system. By reducing pressure to the necessary minimum, energy can be saved and the efficiency of the pump increased.
In addition, choosing the right one also plays a role pump material a crucial role. Depending on the media being pumped, using wear-resistant materials or corrosion resistance can help extend the life of the pump and maintain its performance.
In addition to these technical measures, the training of great importance to the operating staff. This is because correct operation and handling of the pump can contribute to efficient operation and thus to optimum performance. Staff should therefore have the necessary expertise and receive regular training.