Application and function of centrifugal pumps
There are various types of centrifugal pumps that are used depending on the application can be.
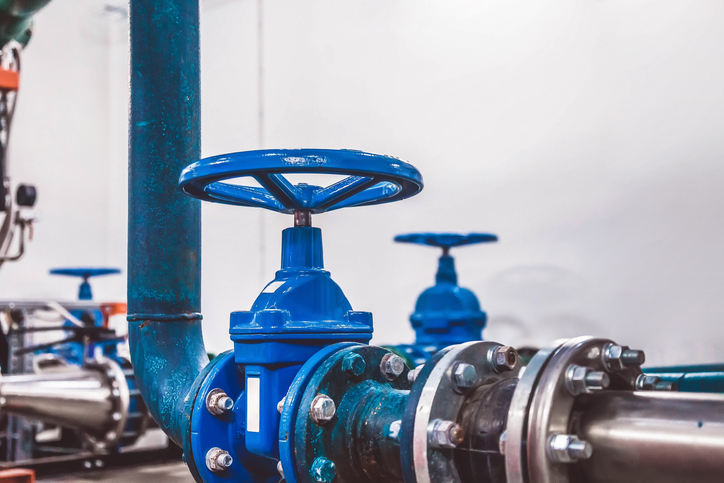
centrifugal pumps are liquid pumps that are used in various industrial and commercial applications. They are characterized by their efficient operation and their ability to transport large quantities of liquids. In contrast to the positive displacement pumps, Where a moving piston or a rotating rotor is used, centrifugal pumps use a rotating disc or propeller to deliver fluid.
centrifugal pumps, too centrifugal pumps , are used in a wide range of industries. This includes water supply, waste water treatment, chemistry, petrochemicals, energy generation, food and beverage industry as well as heating, ventilation and air-conditioning technology. Its main function is to liquids to transport from one location to another, whether from a reservoir to a container, from a tank to a process, or from a river to a treatment plant.
Zu unseren Industriepumpen
What types of centrifugal pumps are there?
There are various types of centrifugal pumps, which differ in their design and operation. Here are some of the most common types:
- Single-stage centrifugal pumps: These pumps have only one impeller and are primarily used for low to medium pressure applications. They are good for general water supply systems, irrigation, swimming pools and similar applications.
- Multi-stage centrifugal pumps: These pumps consist of several impellers that are connected in series. Each impeller further increases pressure so that multi-stage pumps can generate higher pressures. They are often used in high-pressure applications, such as high-pressure cleaning, fire extinguishing systems or process industries.
- verticals Centrifugal pumps: These pumps are specifically designed for installation in vertical positions. They have a vertical motor and a vertical shaft, which saves space. As a result, they can be used in specific applications such as wells, shafts or tanks.
- Horizontal Centrifugal pumps: These pumps are the most commonly used centrifugal pumps and have a horizontal orientation. They offer easy maintenance accessibility and are used in a wide range of applications, from water supply systems to industrial processes.
- Self-priming centrifugal pumps: These pumps are able to draw in liquid from a low level without the need for pre-suction. They are particularly useful in applications where the source of liquid is not always above the pump, such as when draining excavation pits or when handling dirty water.
- slurry pumps: These special centrifugal pumps are designed to pump slurry, sludge, or abrasive liquids. They have robust designs and durable materials to handle abrasive wear. Slurry pumps are used in the mining industry, wastewater treatment, and other areas where conveying solid particles is required.
How do centrifugal pumps work?
The functioning of centrifugal pumps is based on the principle of centrifugal force.
During pump operation, the liquid to be pumped enters the pump via the inlet.
Inside the pump system is the impeller, which is also known as an impeller. The impeller is a disc-shaped structure with curved blades. It is mounted on a shaft and is driven by a motor or other drive source.
When the motor is turned on, the impeller starts to rotate at high speed.
As a result of the rotation, the impeller generates centrifugal force.
The centrifugal force forces the liquid outwards from the center of the impeller.
The liquid is captured by the curved blades and caused to move tangentially outwards.
The pressure of the liquid is increased by the centrifugal force and the tangential movement of the impeller.
This Pressure increase drives the liquid through the pump and through the outlet pipe where the pump is installed.
The pumped liquid leaves the pump via the outlet and can be transferred to the desired application.
It is important to note that centrifugal pumps operate continuously and do not have a discrete delivery cycle such as positive displacement pumps. They generate a continuous flow rate based on the rotation of the impeller and the associated centrifugal force.
The efficiency and performance of a centrifugal pump can be influenced by various factors. This includes the pump design, the diameter of the impeller, the speed of rotation, the viscosity the liquid and other operational parameters. Die Selecting the right pump For a specific application, these factors must be considered in order to achieve optimal results.
In which areas and industries are centrifugal pumps used?
Centrifugal pumps are used in a wide range of areas and industries.
Centrifugal pumps are used in water supply to pump water and deliver it to households, buildings or industrial plants.
In HVAC systems, they are used to circulate the coolant or heating medium.
In the process industry, they are used to transport liquids in production processes.
In wastewater and treatment technology, they are used to pump, treat and transport waste water.
In agriculture, centrifugal pumps are used for irrigation, irrigation and transportation of liquid fertilizers.
In the oil and gas industry, they are used to extract crude oil, water injection, gas compression and transport of liquids.
In shipbuilding and the navy, they are used to cool, pump out bilge water and supply various systems with water.
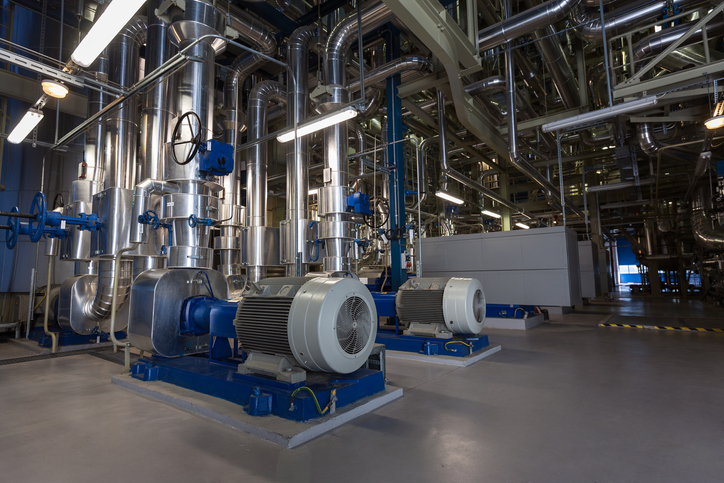
What is the difference between centrifugal pumps and positive displacement pumps?
In addition to the mode of operation and pump technology, positive displacement pumps and centrifugal pumps differ in particular in the conditions of the pumped media.
With centrifugal pumps, the flow rate decreases steadily even at a viscosity of 100 cSt. In the case of positive displacement pumps, such as the wobble ring pump One is, does the pump efficiency increase as it increases viscosity. This is because wobbling ring pumps through the wobble ring have a constant delivery pressure can build up, regardless of the viscosity of the pumped medium.
Another difference between positive displacement pumps and centrifugal pumps lies in their ability to build up pressure. Displacement pumps can a constants Build up delivery pressure, regardless of the viscosity of the pumped medium. Centrifugal pumps, on the other hand, can generate a certain amount of pressure, but their ability to build up high pressure is limited. positive displacement pumps are therefore more suitable for applications where a high delivery pressure is required, while centrifugal pumps are generally sufficient for applications with lower pressure.
They also differ in their ability to work with solids to deal with. Positive displacement pumps are generally better suited for handling solids. Thanks to the displacement mechanism, they are able to transport solid particles. Centrifugal pumps have difficulties with solids and can even become clogged or damaged as a result.
In addition, positive displacement pumps are generally better with Gasen avoid and promote them effectively. Centrifugal pumps are less efficient at pumping gases. They may have reduced performance when there is a high gas content in the pumped medium.