Design of a pump
Find out the function and structure of a pump here.
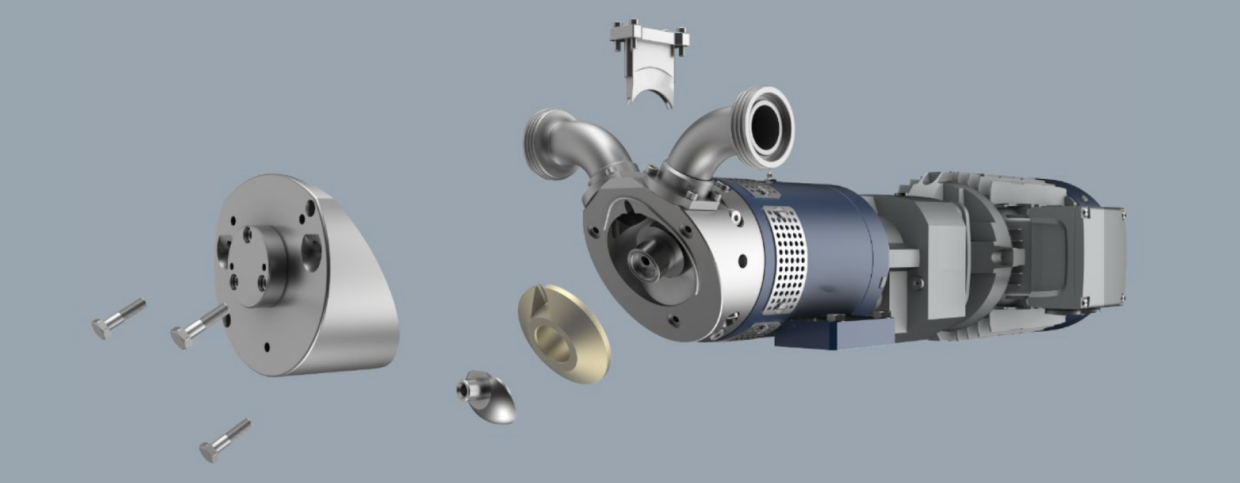
The task of pumps is to transport liquids or gases from one place to another. Pumps are used in many different areas, for example in the water supply, oil and gas industry or chemical industry. Here You can find other areas of application for our pumps. However, the basic structure of a pump is always similar. You can find out exactly how a pump is set up in the following article.
What type of pumps are there?
There are various styles of pumps, which are used depending on requirements and area of application. Among the most common pump types include centrifugal pumps and positive displacement pumps.
The positive displacement pumps also include our wobble ring pump. It is characterized by a rotating wobble ring, which runs in a housing and thus forms chambers. As a result of the wobble ring, the chambers are enlarged and reduced, generating a volumetric flow. This flow rate allows liquids or gases to be transported without affecting their quality. Even highly viscose-like materials are no problem. The wobble ring pump is used in various areas, such as the chemical industry, food processing or medical technology. Thanks to its robust construction and high reliability, the wobble ring pump is a popular and proven pumping system.
You can find out more about the wobble ring pump in our product brochures.
You have the option of choosing your ideal wobbling ring pump flexibly at short notice rent. We are happy to help you find a pump that is tailored to your needs. Feel free to use contact to us uaf.
centrifugal pumps consist of a housing in which a rotating disk is located. This disk has impeller blades which move when the disk rotates and thus generate centrifugal force. Through this working principle The liquids are sucked in and transported through the housing.
Our wobble ring pump
A major advantage of centrifugal pumps is their efficiency. You can high volumes Convey liquids and consume only a small amount of energy. They are also able to transport various types of liquids, be it water, oil or chemicals.
There are various types of centrifugal pumps, such as single-stage and multi-stage pumps. Single-stage pumps have a single impeller, while multi-stage pumps have multiple impellers arranged one behind the other in the pump housing. As a result, several pressure increases can be achieved, resulting in a higher conveying capacity leads.
Another difference between single-stage and multi-stage pumps lies in their application. Single-stage pumps are often used for low pressures and large flow rates used, while multi-stage pumps are used for higher pressures and smaller flow rates. As a result, the pressure loss in a multi-stage pump can be better compensated. This is particularly important when the medium to be pumped has to be transported over large differences in height.
How is a pump constructed?
The structure of a pump consists of several basic components. Key parts include the housing, drive mechanism, rotor, and stator.
that housings encloses the other parts of the pump and protects them from external influences. It is usually made of robust material such as metal or plastic. The construction of the housing also has inlet and outlet openings, where the conveyed medium can enter and exit. Easy cleaning of these housings is particularly important in order to transport a variety of different media.
The drive mechanism of a pump is responsible for moving the rotor. This can be caused by various How they work such as an electric motor or a manual crank. A gasoline-powered pump is useful when there is no power supply. For example, in agriculture or construction. The drive converts energy and drives the rotor, which in turn makes the medium move.
The rotor is the rotating part of the pump. It consists of several blades or blades that capture the medium and transport it through the pump. The rotor is mounted inside the housing and rotates due to the drive. The shape and arrangement of the blades or blades may vary depending on the type of pump. The rotor is the heart of the pump. It ensures that a centrifugal force is created, which in turn sets the medium in motion. It is particularly crucial for energy efficiency and power the pump.
The stator is the stationary counterpart to the rotor. It consists of windings or coils which generate a magnetic interaction with the rotor. This interaction makes it possible for the rotor to be set in motion. The stator is firmly connected to the housing and ensures that the rotor remains in a specific position.
In addition to these basic components, pumps can also have various additional parts. These include seals, valves, filters or pressure regulators, for example. These additional parts are used to pump output to optimize and control the medium. Or even changing the direction of conveying. Because depending on the area of application, a different structure is decisive.
Overall, the various components of a pump are closely linked to ensure effective and reliable delivery of the medium. The correct selection of the structure and combination of these components is crucial. So can the operation and ensure that the desired performance is achieved. Pumps are used in many different industries and areas of application used. For example in industry, agriculture, water supply or food processing. Depending on requirements and area of application, different pump types and sizes are used.
The selection of the appropriate pump depends on various factors. For example, the flow rate, the delivery pressure, the type of funding Mediums and local conditions. It is important to analyse the specific requirements and select the appropriate pump to ensure efficient and reliable delivery.
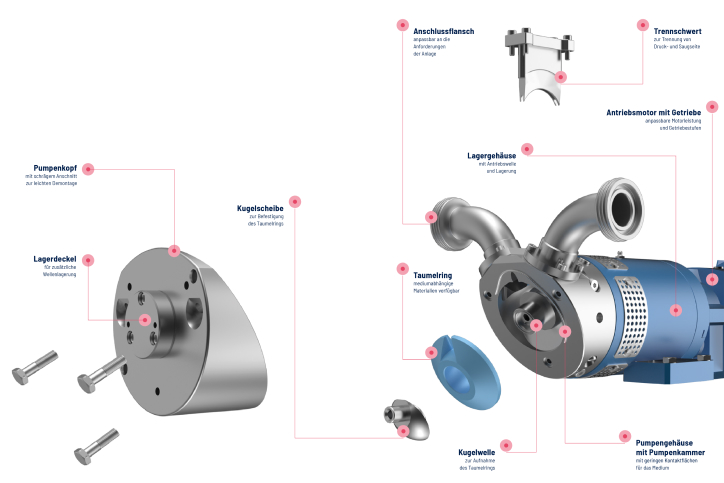
How does pressure build up in a pump?
The Pressure build up In a pump, it is carried out by a combination of different mechanisms. First, a vacuum is generated by the rotation of a shaft or a rotor in the pump. This negative pressure causes the medium to be pumped, for example liquid or gas, to move into the pump's inlet channel. You can therefore speak of suction.
The medium is then sucked into the pump body through the inlet channel. There, it is transported further through various chambers or rotor blades, depending on the type of pump.
As a result of the rotation of the shaft or the Rotors The medium is then compressed and pressurized. This is done by the volume the chambers or the gaps between the rotor blades are reduced. As a result, the medium is pushed into the pump's outlet channel. The centrifugal force plays a decisive role here.
The pressure build up in a pump can also be caused by additional components such as valves or membranes be supported. These ensure that the medium can only flow in one direction and prevent it from flowing back. As a result, the pressure in the pump is maintained and the medium can be pumped continuously.
Depending on the area of application and the desired flow rate, there are various types of pumps, such as centrifugal pumps, piston pumps or diaphragm pumps. Each type of pump has its specific advantages and disadvantages and is suitable for different areas of application.
Building up pressure in a pump is a crucial process for pumping media efficiently and in a controlled manner. By combining various mechanisms and components, pressure is created and maintained to move the medium in the desired direction.